Voltage Endurance Tests on Stator Coils and Bars
High voltage stress causes aging of stator winding insulation and eventually leads to insulation failures. Voltage endurance testing is used as a measure of quality by applying a much higher than normal machine-operation stress (3.76 times higher than the operating phase-to-ground voltage) to coils/bars within a short period of time to accelerate insulation aging which occurs during machine service. Voltage endurance testing has been the most popular accelerated aging test to check the quality of coils/bars for over 30 years.
Voltage endurance tests are performed in accordance with IEEE1043 and IEEE1553-2002. While IEEE1043 essentially defines the procedure for performing voltage endurance tests, IEEE1553-2002 specifies the test parameters and acceptance criteria. For example, a 13.8 kV coil under voltage endurance testing conditions requires applying a 30 kV voltage to the coil for 400 hours while maintaining them at around 100˚C temperature. The coil should pass the 400-hour test without failures. The number of specimens for voltage endurance test shall be at least four bars or two coils, but not more than 1% of the number of bars/coils in the winding.
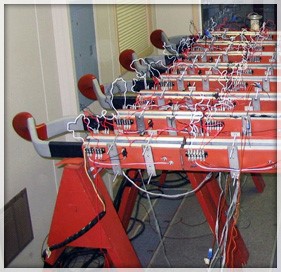
IEEE1553-2002 specifies the pass/fail criteria. If less than 26% of the specimens tested fail between 51% and 100% of the minimum time-to-failure, then 2 additional bars/coils shall be tested. All these remaining specimens must pass the test.
If coils/bars fail a voltage endurance test, a failure investigation including dissection of the failed coils/bars is conducted. Manufacturers should take remedial actions to fix the problems and make a new set of coils/bars for re-testing until the coils/bars pass voltage endurance test. If the coils/bars are not able to pass the voltage endurance test, the whole set of production coils/bars could be rejected.
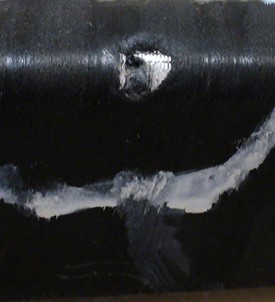
In association with a voltage endurance test, the following diagnostic tests can be performed to assess the insulation quality:
- Insulation resistance and polarization index
- Tap test: A small piece of metal (e.g. a coin) is used to tap a coil/bar. When a hollow or dampened sound appears, this is indicative of a delaminated insulation
- Dissipation factor (power factor)
- Partial discharge
- Surface resistivity: A test is to check if surface resistance is within a proper range
- Turn-to-turn insulation: A HV impulse is applied to a coil to check the quality of turn-to-turn insulation according to IEEE522
- Insulation breakdown: A destructive test to check dielectric breakdown strength of the groundwall insulation
- Dissection and microscopic examination
Voltage endurance testing has been successfully used to assess the quality of coil manufacturing. A utility had a study to comparing the failure rate of generator insulation before and after they used the quality assurance test program described here. The test program helped the utility to discover many issues of the coil quality and gave them an opportunity to fix issues before installation of the coils in their generators. It was concluded that the insulation failure rate of their generators dropped dramatically after they used the quality assurance test program as a part of their specification for purchasing a new set of coils/bars during last 20 years.
Many generator owners prefer to get voltage endurance testing done by an independent test laboratory.